Пластикалык форма менен куюу - бул пластикалык калыпка салуунун эң кеңири колдонулган түрү. Пластикалык инжектордук формага келтирилген бөлүктөр электрондук, электрдик, электрдик, медициналык, транспорттук, автомобиль, жарыктандыруу, айлана-чөйрөнү коргоо, коопсуздук, тиричилик техникасы, спорттук шаймандар жана башка тармактарда жана буюмдарда колдонулат.
Инъекциялык калыпка салуу деген эмне? Пластикалык сайынуу формасы - бул белгилүү бир температура диапазонунда тетиктерди өндүрүү процесси, бурап толук эриген пластмасса материалдарын аралаштырып, жогорку басым менен форма көңдөйүнө куюп, муздатып, айыктыргандан кийин, калыпка салуу ыкмасын алат. Бул ыкма татаал бөлүктөрдү партия менен чыгарууга ылайыктуу жана иштетүүнүн маанилүү ыкмаларынын бири. 6 баскыч бар: көктү жабуу, эритилген пластмасса сайуу, басымды кармоо, муздатуу, калыпты ачуу жана продукт алуу. Ылдамдык, басым, позиция (инсульт), убакыт жана температура инъекциялык калыпка салуунун 5 негизги элементи болуп саналат.
Инъекция жасоочу бирдиктин үч элементи
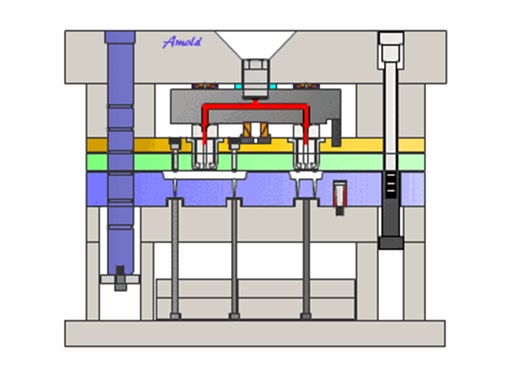
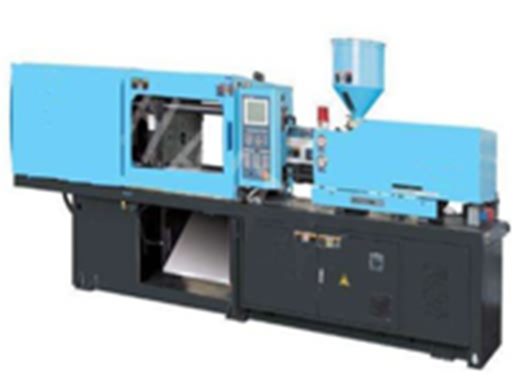
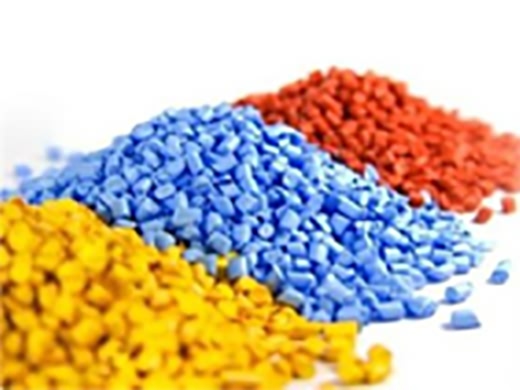
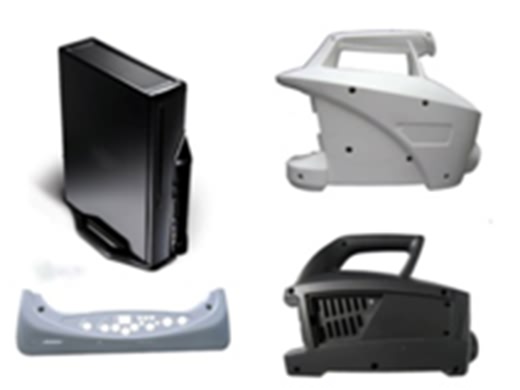
Инъекциялык формадагы буюмдарды колдонуу
(1) Электроника өнүмдөрүндө:. Байланыш электрондук буюмдары жана турмуш-тиричилик электроникасы (пластикалык корпус, корпус, кутуча, мукаба) Уюлдук телефондор, наушниктер, телевизорлор, видео телефондор, POS машиналар, эшиктин коңгуроосу.
(2) тиричилик техникасында: Кофе бышыргыч, шире салгыч, муздаткыч, кондиционер, желдеткич шайба жана микротолкундуу меш
(3) Электр жабдууларында: Электр эсептегич, электр кутучасы, электр шкафы, жыштык өткөргүч, жылуулоо капкагы жана ачкыч
(4) Медициналык жана саламаттыкты сактоо жабдыктарында жана шаймандарында: Иштетүүчү лампалар, сфигмоманометр, шприц, тамызгыч, дары бөтөлкөсү, массажер, чачты кетирүүчү шайман, фитнес жабдуулары
(5) автомобилде: панелдин корпусунун каркасы, батарея кронштону, алдыңкы модуль, башкаруу кутучасы, отургучту колдоо рамасы, запастык плацента, фендер, бампер, шасси капкагы, ызы-чуу тосмосу, арткы эшиктин алкагы.
(6) Өнөр жай жабдыктарында: Машиналар панели, редуктор, которуштуруу, жарык берүү.
(7) Кыймылдаткыч жана унаа каражаттары (чырактын капкагы, тосмо) Сигнал лампасы, белги, спирт ичимдиктерин текшерүүчү.
Инъекция жасоочу бирдиктин үч элементи
Көктүн, инжектордук формадагы машинанын жана пластмасса чийки заттардын максаты инъекциялык калыптын негизги бирдигин түзөт. Көк жана инжектордук калыпка келтирүүчү машина өндүрүш жабдуулары болуп саналат, ал эми желим чийки зат продукт материалын түзүү үчүн колдонулат.
1. сайма формалар
Инъекциялык көктүн түрү - бул пластмассадан жасалган буюмдарды өндүрүүчү шайман; бул ошондой эле пластикалык буюмдарга толук структура жана так өлчөм берүүнүн куралы. Инъекциялык калыпка салуу - бул кээ бир татаал бөлүктөрдү сериялап чыгарууда колдонулуучу иштетүүнүн бир түрү. Тагыраак айтканда, эриген пластмассаны формага куюп куюучу машина жогорку басым менен куюп, калыпка салган продукт муздатып, айыктыргандан кийин алынат. Injection көкту ар кандай көктүн түзүлүшү, продукт дизайн талаптары, өндүрүш режими жана орнотуу жана пайдалануу режими боюнча ар кандай түрлөрүнө бөлүүгө болот.
Калыптардын өндүрүү баасы жогору болгондуктан, алардын узак иштөө мөөнөтү жана өндүрүштүн эффективдүүлүгү жогору болгондуктан, алар адатта массалык өндүрүш үчүн гана колдонулат. Инъекциялык калып пластикалык бөлүктөрдү массалык түрдө өндүрүү үчүн колдонулат. Көгөрүп кетүү чыгымдарын бөлүштүргөн жогорку натыйжалуу пластмасса буюмдарынын саны, ошондуктан бир продуктту инжекциялык калыпка чыгаруунун чыгымдары башка иштетүү ыкмаларына караганда бир кыйла төмөн. Калыпты иштеп чыгуу жана калыпты текшерүү үч этаптан турат.
(1) көктүн дизайны:
Көктүн дизайны продукциянын дизайнына, дизайн программасынын колдонулушуна, механикалык иштетүүнүн жана инжектордук калыпка куюу процесстеринин мүнөздөмөлөрүнүн калыптарына, бүтүндөй калып механизминин дизайнына, бөлүктөрүнө ылайык келтирилген.
(а) Биринчи кадам - пластмассадан жасалган буюмдардын дизайнын талдоо
б) Экинчи кадам - матрицанын материалын тандоо
(в) Үчүнчү кадам - көктүн механизмин иштеп чыгуу
(г) Төртүнчү кадам - көктүн тетиктерин иштеп чыгуу
(2) көктү иштетүү
Көк иштетүү негизинен механикалык иштетүү аркылуу Чиймени карап чыгуу → материалдарды даярдоо → иштетүү → көктүн негизин иштетүү → көктүн өзөгүн иштетүү → электродду иштетүү → көктүн бөлүктөрүн иштетүү → текшерүү → монтаж → учуучу көк → сыноо формасы → өндүрүү
Инъекциялык көктүн иштетүү цикли көктүн татаалдыгына жана иштетүү деңгээлине жараша болот. Жалпы өндүрүштүк цикл 20-60 жумушчу күндү түзөт. Көк иштетүүдө колдонулуучу машина: CNC, токардык станок, жалпы фрезердик станок, бет майдалагыч, EDM, WEDM, ошондой эле кол шаймандарын, өлчөө шаймандарын ж.б.
(3) Инъекциялык калыптардын түрлөрү:
Инъекциялык көкту калыптын түзүлүшүнө, продукциянын дизайн талаптарына, өндүрүш режими жана орнотуу жана колдонуу режимине ылайык ар кандай түрлөргө бөлүүгө болот.
(а) Эки табак калып: инжектордук калыпта кыймылдуу калып жана калыптын туруктуу формасы бөлүнүп, андан кийин пластмасса бөлүктөрү чыгарылат, ал эки табакчалуу калып деп да аталат. Бул абдан жөнөкөй жана фундаменталдык пластмасса сайынуу формасы. Бул суроо-талапка ылайык, бир көңдөй сайынуу көктүн же көп көңдөй сайынуу көктүн катары иштелип чыккан болушу мүмкүн. Бул көп колдонулган сайынуу көкту болуп саналат. Бир же көп көңдөйдүү инжекциялоо үчүн калып,
б) Үч табактуу калып: эки жолу бөлүнүп кетүүчү калып деп да аталат. Бир бөлүктөн турган сырткы инжектордук көк формага салыштырмалуу, экиге бөлүнгөн инжекциялык калып, чекит дарбазасы үчүн туруктуу калыптын курамдык бөлүктөрүндө жарым-жартылай кыймылдуу стриптер кошот. Комплекстүү түзүлүшү жана өндүрүштүк баасы жогору болгондуктан, ири бөлүктөрдүн калыптарында колдонулбайт.
(в) ысык чуркоочу калып: ысык чуркоочу калып жылуулук приборун колдонуп, каналдагы эритүү дайыма катып калбашы үчүн колдонулат. Бул салттуу көгөрүп чыгарууга караганда кыйла натыйжалуу жана чийки затты үнөмдөгөндүктөн, азыркы өнүккөн өлкөлөрдө жана аймактарда ысык жөө күл формасы кеңири колдонулат. Ысык чуркоочу тутумунда кадимки калыпка караганда дагы бир ысык чуркоочу тутум бар, ошондуктан чыгым жогору.
(г) Эки түстүү көктүн түрлөрү: жалпысынан бир эле инжектордук формадагы машинадагы инжекциялык калыпка салынган эки түрдөгү пластмассадан жасалган материалдар, эки калыпташтыруу деп аталат, бирок продукт бир гана жолу калыпка салынат. Жалпысынан, бул калыпка салуу процесси, адатта, бир калыптын жыйындысы менен бүтүрүлүп, эки түстүү инжекциялоо үчүн атайын машинаны талап кылган кош инжекциялоо деп аталат.
(4) Инъекциялык көктүн курулуш подсистемасы төмөнкүдөй
Инъекциялык калып жалпысынан төмөнкү подсистемалардан турат:
(а) Дарбазалар тутуму. Бул формадагы пластикалык агым каналын сайуучу форсункадан көңдөйгө билдирет. Жалпы эшик системасы спрю, дистрибьютер, дарбаза жана муздак тешиктен турат.
б) Капталдан бөлүү жана өзөктү тартуу механизми.
(c) жетектөөчү механизм. Пластикалык калыпта, ал негизинен кыймылдоочу жана белгиленген көктүн жабылышынын тактыгын камсыз кылуу үчүн жайгаштыруу, жетектөө жана белгилүү бир каптал басымын көтөрүү функциясына ээ. Өлүп жабылуучу багыттоочу механизм жетектөөчү түркүктөн, жетектөөчү жеңден же жетелөөчү тешиктен (шаблондо түздөн-түз ачылган) жана жайгаштыруучу конустун бетинен турат.
(г) Чыгуу / демонтаждоо механизми. Анын ичинде түртүп чыгаруу жана өзөктү тартуу механизми. Ал негизинен бөлүктөрдү калыптан чыгаруу үчүн колдонулат. Ал эжектордук таякчадан же түтүктү айлантуудан же түртүп салуучу плитадан, эжектордук плитадан, эжектордук таякчадан бекитилген плитанын, баштапкы абалга келтирүүчү таяктан жана тартуучу таяктан турат.
(e) Температураны көзөмөлдөө тутуму. Муздатуучу жана жылытуучу шаймандар.
(f) Чыгуу тутуму.
(ж) Калыптоочу бөлүктөр көктүн көңдөйүн түзгөн бөлүктөргө карата колдонулат. Ал негизинен төмөнкүлөрдү камтыйт: перфоратор, ургаачы өлөт, өзөк, форма таякчасы, шакек жана киргизгич.
(з) Бекитилген жана орнотулган бөлүктөр. .
(5) Калыптарга арналган материал
Пластикалык калыпка термопластикалык калып жана термореактивдүү пластикалык калып кирет. Пластикалык калып үчүн болоттон жасалган бекемдик, катуулук, эскирүү, жылуулукка туруктуулук жана дат басууга туруктуулук сыяктуу белгилүү бир касиеттер талап кылынат. Мындан тышкары, кичинекей жылуулук менен иштөө, иштетүүнүн натыйжалуулугун жогорулатуу, коррозияга чыдамдуу болуу, жылмалоо жана жылтыратуу өнүмдөрүн жакшыртуу, ширетүү өндүрүмдөрүн оңдоо, жогорку катаалдык, жылуулук өткөрүмдүүлүгү жана туруктуу иштөө көлөмү жана формасы шарттары.
Кандай формадагы сайма материалы колдонулат, ал калыптын болотун тандоого чоң таасир этет. Эгерде арматуралоочу агент же башка модификациялоочу агент, мисалы, айнек буласы кошулган болсо, анда калыпка чоң зыян келтирилгендиктен, материалды тандоону ар тараптуу караш керек. Күчтүү кислота пластиктен жасалган материалдар PVC, POM, PBT; алсыз кислота пластик материалдары PC, PP, PMMA, PA. Адатта, күчтүү дат басуучу пластиктер үчүн S136, 1.231, 6420 жана башка формадагы болоттор тандалат, ал эми алсыз дат басуучу пластиктер үчүн S136, 1.2316420, SKD61, NAK80, pak90718 ж.б. Өнүмдөрдүн сырткы көрүнүшүнө болгон талаптар көктүн материалдарын тандоого чоң таасирин тийгизет. Күзгү бетин жалтыратуучу тунук бөлүктөр жана буюмдар үчүн S136, 1.2316718, NAK80 жана пак90420 материалдары бар. Ачыктыктын жогорку талаптары менен калып S136 тандап, андан кийин 420 тандалышы керек. Эгерде продукт талаптарын баасын жана чыгымдарын эске албастан гана канааттандырса, анда мыкты дизайнер болбой калышы мүмкүн, ошондой эле көк өндүрүү наркы да биринчи орунда турат
2.1njection калыпка жабдуулар
(1). Инъекциялык формадагы машина:
бул термопластикалык же термореактивдүү пластмассаны пластикалык калыптан ар кандай формага пластикалык формага келтирүү үчүн негизги формага келтирүүчү жабдуу Горизонталдуу форма куючу машина, вертикалдык инжекциялоо үчүн машина, эки түстүү инжекциялоо үчүн машина, толук электрдик инжекциялоо үчүн машина Бирок, кандай гана болбосун формациялоочу машина, анын негизги функциялары эки:
а) Пластмассаны эритүү үчүн ысытыңыз.
б) Эритилген пластикке көңдөйдү чыгаруу жана толтуруу үчүн жогорку басым жасалат. Инъекциялык формага келтирүүчү машинанын негизги параметрлери: кысуу күчү, инжекциянын максималдуу көлөмү, калыптын максималдуу жана минималдуу калыңдыгы, кыймылдуу инсульт, суурма аралыгы, эжекция инъекциясы жана эжекция басымы. Ар кандай өлчөмдөгү, конструкциядагы жана материалдардагы бөлүктөр үчүн, ошондой эле ар кандай көлөмдөгү жана типтеги калыптар үчүн, инжектордук калыпка салуучу машиналардын ар кандай моделдери жана параметрлери тандалышы керек. Толугу менен электр инжектордук калыпка салуу машинасы жогорку саюу ылдамдыгынын, так башкаруунун жана өндүрүштүн натыйжалуулугунун артыкчылыктарына ээ. Айрым так бөлүктөрдү ийне менен куюу үчүн колдонулат.
(2) Көмөкчү жабдуулар:
(а) Инъекциялык калыпка салуучу машинанын манипулятору - бул адамдын жогорку буттарынын кээ бир функцияларын туурап, автоматтык түрдө өндүрүш жабдуулары жана алдын-ала белгиленген талаптарга ылайык буюмдарды ташуу же шаймандарды иштетүү үчүн аны автоматтык түрдө башкара алат. Манипулятор иштөө циклинин ырааттуулугун камсыз кылып, сапатын жакшыртып, коопсузураак кыла алат. Кытайда пластмассаны кайра иштетүү өнөр жайынын тез өнүгүшү менен, инжектордук формадагы жабдууларды автоматташтыруу деңгээли барган сайын жогорулоодо. Заманбап инжекциялоочу машиналар өндүрүштүн натыйжалуулугун жогорулатуу үчүн көп учурда манипуляторлор менен жабдылган.
(б) Май жылыткыч / суу муздаткыч: калыптан аккан суюктук аркылуу ысытуу же муздатуу, көктүн температурасын жогорулатуу, беттин сапатын жогорулатуу же өндүрүмдүүлүктү жакшыртуу үчүн көктүн температурасын тез төмөндөтүү.
(в) Кургатуучу кургаткыч: ысытуу жана үйлөө менен желим материалдардан нымдуулукту кетирүү.
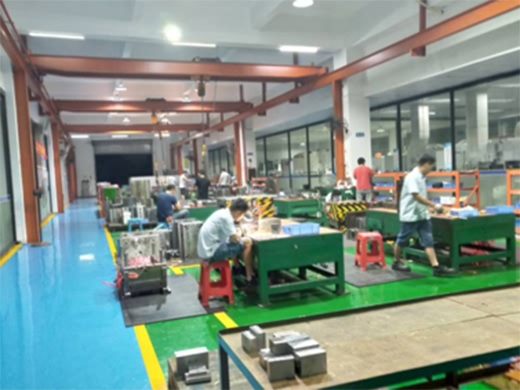
Инъекциялар үчүн форма куюучу цех
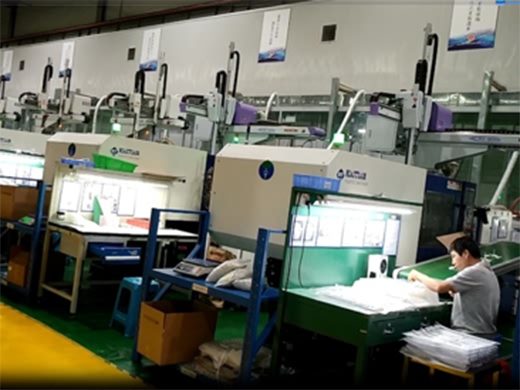
Инъекциялар үчүн калыптарды чыгаруу линиясы
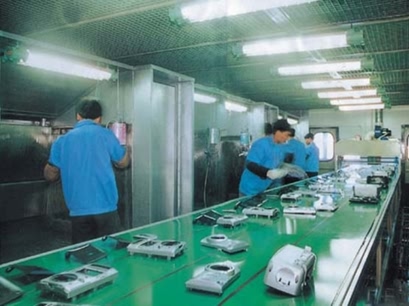
Пластикалык бөлүктөрдү сырдоочу линия
3. Пластикалык материалдар
Инъекциялык калыпка салууда колдонулуучу пластикалык чайырлар: Төмөндө инъекциялык калыпта колдонулган эң кеңири тараган термопластиктер келтирилген: Акрилонитрил бутадиен стиролу, акрилонитрил бутадиен стиролу (ABS), тунук эмес термопластикалык жана аморфтуу полимер. ... Полиэтилен. ... Поликарбонат. ... Полиамид (Нейлон) ... Таасири күчтүү Полистирол. ... Полипропилен
Материал | Тыгыздык | Көк Кысуу |
Өзгөчөлүгү | Колдонмо |
Грам / см3 | % | |||
ABS(Акрилонитрит бутадиен стирол) | 1.04 ~ 1.08 | 0.60 | Туруктуу көлөм, жакшы комплекстүү механикалык касиеттер,оңой электропластинг, оңой форма менен куюу | электрондук буюмдар үчүн пластикалык корпус |
PC (Поликарбонат) | 1.18 ~ 1.20 | 0.50 | Жакшы таасир күч, туруктуу көлөмү жана жакшы жылуулоо.Начар коррозияга жана эскирүүгө туруктуу | пластикалык корпус, коргоочу каптама, электрондук буюмдар, электр буюмдары үчүн чакан берүүчү бөлүктөр |
PMMA(Полиметилметакрилат) | 1.17 ~ 1.20 | 0.60 | Ал 92% жакшы өткөрүмдүүлүккө ээ жана ар тараптуу механикалык күчкө ээ.Тиштин таасиринин күчү төмөн, стрессте жеңил | Аспаптын тунук линзалары жана дисплейдеги терүү белгилери |
PP(Полипропилен) | 0,89 ~ 0,93 | 2.00 | Ал жогорку кичирейүү, нымга туруштук берүү,жогорку температурага туруштук берет жана аны айрып алуу оңой эмес.Low Wear каршылык, карылыкка оңой, төмөнкү температуранын начар иштеши | Тамак-аш идиштери, идиш-аяк, микротолкундуу мештин кутучалары, медициналык контейнерлер |
(хлорид) | 1.38-1.41 | 1.50 | Катаал, эскирүүгө туруктуу, жакшы изоляция, кыйла татаал, начар температуранын жогорку көрсөткүчтөрүн түзөт | Түтүктөрдү жана профилдерди жасоо |
Нейлон | 1.12 ~ 1.15 | 0.7-1.0 | Катуу, эскирүүгө туруктуу, сууга туруктуу, чарчоого туруктуу, жакшы изоляция. Жогорку кысылуу, багыттуу | Машина бөлүктөрү, химиялык бөлүктөр, берүү бөлүктөрү |
POM (Polyacetel) | 1.42 | 2.10 | Мыкты механикалык касиеттер, жогорку күч жана катуулук, эскирүү жана соккуга туруштук берүү. Термикалык туруктуулук начар | Машина бөлүктөрү, химиялык бөлүктөр, бөлмө температурасында иштеген трансмиссия бөлүктөрү, сүрүлүү бөлүктөрү жана берүү бөлүктөрү |
TPU(Термопластикалык полиуретан) | 1.05 ~ 1.25 | 1.20 | Эластомер, эскирүүгө туруктуу, майга чыдамдуу, жогорку жана төмөнкү температуранын ийкемдүүлүгү, уулуу эмес | Медицинада, тамак-ашта, электрондук өнүмдөр жана төмөнкү температура чөйрөсү |
Инъекциялык калыпка салуу процесси - бул эриген чийки заттарга басым жасап, сайып, муздатып, бөлүп, жарым-жартылай даяр бөлүктөрдүн белгилүү бир формасын алуу процесси. Пластикалык бөлүктөрдүн жалпы инжекциялык калыпка салуу процесси негизинен 7 этапты камтыйт. : Параметрди коюу -> көктүн жабылышы-> толтуруу -> (газдын жардамы менен, суунун жардамы менен) басымдын сакталышы -> муздатуу -> көктүн ачылышы -> демонтаж.
Ылдамдык, басым, позиция (инсульт), убакыт жана температура инъекциялык калыпка келтирүү процессинин беш негизги параметрлери болуп саналат. Инъекциялык формадагы өндүрүштө, негизинен, квалификацияланган көлөмдү жана сырткы көрүнүштү өркүндөтүү жана алуу үчүн ушул параметрлерди оңдоо керек.
Жети типтүү инжекциялык калыпка салуу технологиясы
1. Кош инжекциялуу калыпка салуу
2. Ашыкча калыпка куюу
3. ысык чуркоочу сайынуу калыпка салуу
3. IMD: формада жасалгалоо саймасы
4. Ири бөлүктөргө ийне саюу
5. Айрым бөлүктөрдү ийне менен калыпка салуу
6. Автомобилдердин тетиктерин инжектордук калыпка салуу
7. Жука дубал бөлүктөрүн сайуу
Кийинки иштетүү
Биз сиздин пластикалык сайынуу калыпташкан бөлүктөрүн ар кандай стандарттуу сайма куюлуучу полимерде жана сиз талап кылган 0.1gram-10kgs көлөмүндө камсыз кыла алабыз. Мындан тышкары, биз сиздин оюнду кесипкөй аягына чейин берүү үчүн, оюк салынуучу киргизгичтерди, металл каптоочу туташтыргычтарды же башка пластикалык инжектордук формадагы бөлүктөрдү ашыкча калыпка сала алабыз. Пластикалык инжектордук калыпка келтирүү кызматтарынын бир бөлүгү катары суб-жыйындар түзүлүп, сиздин талаптарга ылайык топтолушу мүмкүн. Ушул эле ар кандай бүтүрүү процесстерине тиешелүү, анын ичинде:
* Пластмассадан жасалган хром менен каптоо
* Живопись
* Санарип сүрөт
* Төшөктөрдү басып чыгаруу
* RF коргонуу
* Таңгак жана таңгак
* Инъекциялык калыптын сапатын көзөмөлдөө Биз ошондой эле тез шаймандарды, прототиптөө жана калыптан кийинки кызматтарды сунуштайбыз.
Калыптагы кемчиликтер жана көйгөйлөрдү чечүү
Калыпка салгандан кийин, пластмасса бөлүктөрү менен алдын-ала белгиленген сапат стандарттарынын (инспекциянын стандарттары) ортосунда айрым айырмачылыктар бар, алар кийинки процесстин талаптарына жооп бере албайт. Бул көбүнчө сапаттагы көйгөйлөр деп аталган пластикалык бөлүктөрдүн кемчиликтери. Биз бул кемчиликтердин себептерин изилдеп, аларды минимумга чейин азайтышыбыз керек. Жалпылап айтканда, бул кемчиликтер төмөнкү аспекттерден улам келип чыгат: калып, чийки зат, процесстин параметрлери, жабдуулар чөйрөсү жана персонал.
1. Жалпы кемчиликтер:
(1). Түстөрдүн айырмасы: эгерде инжектордук формага келтирилген бөлүктөрдүн түсү жылаңач көздөрдүн бирден-бир түстүү үлгүсүнөн айырмаланса, анда ал стандарттуу жарык булагындагы түс айырмасы катары бааланат.
(2). Толтуруу жетишсиз (желимдин жетишсиздиги): сайма калыпка салуучу бөлүктөрү толук эмес, жана кадимки шаблонго туура келбеген көбүкчөлөр, боштуктар, кичирейген тешиктер жана башкалар бар, ал желимдин жетишсиздиги деп аталат.
(3). Деформациянын деформациясы: пластмассадан жасалган бөлүктөрдүн формасы демортация болгондон кийин же кийинчерээк айланып, буралат. Эгерде түз каптал ичкери же сыртка караса, же жалпак бөлүктүн өйдө-ылдый жактары болсо, эгерде буюмдун таманы тең болбосо, аны деформация деп аташат, аны жергиликтүү деформация жана жалпы деформация деп бөлүүгө болот.
(4). Ширек сызыгынын белгилери (сызыктары): пластмасса бөлүктөрүнүн бетиндеги сызыктуу издер, формада пластмассалардын эришинен пайда болот, бирок эриштер кесилишинде толук эришпейт, андыктан аларды бир бириге бириктирүүгө болбойт. Алар негизинен түздөн-түз сызык болуп, тереңден тайызга чейин өнүгүшөт. Бул көрүнүш сырткы көрүнүшүнө жана механикалык касиеттерине белгилүү бир таасирин тийгизет.
(5). Риппл: сайма формасында куюлган бөлүктөрдүн бетинде спираль же булут бар, же тунук буюмдун ичи толкундуу оймо-чиймеге ээ, ал толкундуу деп аталат.
(6). Үстүнөн (жарк, Кейп).
(7). Өлчөмдүн дал келбестиги: калыпка келтирүү процессинде куюлган формадагы бөлүктөрдүн кичирейиши жана бузулушу
2. Сапатты көзөмөлдөө жана өркүндөтүү: Ага технология жана менеджмент кирет
(1). Техникалык деңгээл: материалдарды туура тандоо, продукциянын структурасынын дизайны, ылайыктуу көктүн материалдарын тандоо, толтурууну жеңилдетүү үчүн калыптын түзүлүшүн оптималдаштыруу, түтүндү чыгаруу жана бөлүктөрдү кетирүү, бөлүү бетинин, агым каналынын жана резина киришинин акылга сыярлык орнотулушу; өнүккөн сайынуу калыпка жабдууларды пайдалануу же жараяны.
(2). Башкаруу деңгээли: келип түшкөн материалдардын сапатын контролдоо, сапаттуу саясатты жана стандарттарды иштеп чыгуу, техникалык окутуу, процесстин акылга сыярлык мүнөздөмөлөрүн түзүү, маалыматтарды жазуу жана талдоо, сапаттуу тутумду түзүү.
Mestech компаниясы жылына жергиликтүү жана дүйнө жүзү боюнча кардарлар үчүн жүздөгөн калыптарды жана миллиондогон пластмасса буюмдарын чыгарат. Эгерде сиз көбүрөөк билгиңиз келсе же пластикалык инжекциялоо формасы жөнүндө котировка жөнүндө билгиңиз келсе, анда бүгүн биз менен байланышыңыз.